The government’s 2025 vision for construction is compelling and challenging: 33 per cent lower costs; 50 per cent faster delivery; 50 per cent lower emissions; and 50 per cent improvement in exports.
In other words, in 10 years’ time our construction industry will be so good the rest of the world will be knocking at our door to buy a slice of our expertise.
No pressure then.
Performance improvement of this type will require the industry to throw out the old ways of doing things and start again with a radically different approach.
Tweaking current practice or applying steady continuous improvement techniques will not work at this scale.
Big change needed
Of course we know this has been tried before; the Latham and Egan reports recommended moves towards more integrated supply chains, better design, more efficient working methods and better communication using the technology of the day.
With the exception of a few mega-projects such as Heathrow Terminal 5, the Queen Elizabeth Olympic Park and Crossrail, the rank and file of the industry carried on in its own sweet way.
The core thinking driving the current agenda is that we can create buildings in factories using techniques that have revolutionised the car industry, with minimal onsite labour for final build and commissioning.
This is not new.
I joined the oil and gas sector in the early 1980s where it was quite normal to create plant in a fabrication yard and move it to site to plug it and start up.
These were turnkey projects – they did what they said on the tin.
Lessons from automotive
The automotive industry goes further, sharing common platforms between competitors so that the basic components of the car are the same, with competing companies focusing on innovative design to differentiate their products.
To transform the construction industry into one that can crank out mass-produced components to be assembled in different ways to make different buildings will require root-and-branch reform of the way we look at skills.
The construction professional of the future will work in collaborative teams of experts, will probably be a Six Sigma Black Belt, well versed in lean manufacturing, just-in-time inventory techniques and statistical process control.
Construction companies will compete for talent with Jaguar Land Rover, Toyota and Ford.
So how do we bring about this revolution?
I am honoured to chair the Supply Chain School, which recently launched its Offsite School at the iconic Crystal venue in East London.
Offsite School
The Offsite School builds on a winning formula, the Supply Chain Sustainability School, which has been using web-based diagnostic and prioritisation tools to deliver bespoke, highly relevant e-learning since 2012.
With more than 25 of the UK’s leading contractors, FM service providers and clients, plus over 8,000 supply chain members signed up to date, industry demand for such a ‘go-to’ resource is proven and growing rapidly.
By engaging experts in the fields required and using the purchasing power of main contractors to drive suppliers to the school, the transformation through learning can begin.
For the Offsite School, launched in March 2015 with funding from the UK Commission for Education and Skills, these are early days, but the signs are already there.
With appropriate investment, there is every possibility that the Offsite School will match or exceed the achievements of its sister initiative.
The road to 2025 will not be easy, but offsite may just prove the vehicle to take construction forward.
Shaun McCarthy is chair of the Supply Chain School and a director at Action Sustainability
Source: Construction News
We need to build offsite – but how?
21st May, 2015
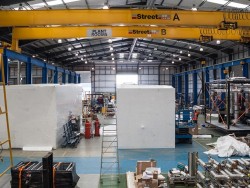