The New Hampton by Hilton hotel at Bristol Airport was the 50th Hampton to open in the UK in 2017, with the success of the scheme largely attributed to the use of volumetric bedrooms built using containerised technology.
The entire 201 bedroom hotel was assembled in less than four weeks, allowing the bedroom areas to be 95-98% complete when the entire construction project was only 50% built. By embracing a modular solution, the design and fabrication of the bedrooms ahead of construction starting on site means that projects could be delivered with a 20-30% saving on programme. The high quality of bedroom finishes achieved as well as the generous public areas at ground floor have delighted the client and operator alike. The bedrooms arrived ready fitted out according to the hotel brand’s exacting requirements, including finished bathrooms, beds, chairs, casegoods, equipment and floor and wall coverings, sourced in China.
Architects Stride Treglown worked with China International Marine Containers- Modular Building Systems (CIMCMBS) engineers in London and China to manage the modular fabrication design development, co-ordinating the structural and mechanical and electrical bedroom areas design for a UK project built by Kier Group.
The use of a container-build bedroom solution was decided before the hotel secured planning approval which delivered the best results for modular design and for the owners, who are the parent company of the modular system. Early engagement with the modular supplier is a key factor in making a success of modular systems, coupled with a hotel design of two simple rectangular bedroom blocks linked by a glazed corridor on three levels.
The 201/251 phased design allows for an additional 50 bedrooms to be added to the hotel as passenger numbers and hence hotel occupancy increase – an ideal build solution for a hotel to remain trading for the duration of the fast-track installation. The façade cladding solution was also adapted to suit the module structure, making use of longspan aluminium composite panel solution to achieve an insulated and watertight façade as soon as practicable. The façade treatments were then applied over this external skin. The typical volumetric module consists of a bespoke section through the building – a completed bedroom/ unfurnished corridor/ completed bedroom that are stacked and bolted together onsite in a matter of weeks, designed according to the exacting hotel chain brand standards with consistently high quality finishes. CIMC as container modular provider were also the developer and owner of the final scheme.
Branded hotels as a building type are well suited to modular prefabrication because of the high degree of repetition. With the rectangular plan form of two simple linear bedroom blocks linked by a striking glazed walkway, as well as bedroom windows centrally located in the external wall, the project was ideally suited to modular. The ground floor bedrooms, not being as tall as the adjacent transfer deck presented an engineering challenge to the stackable solution but careful co-ordination and planning of the steel spacer frame to ensure all first floor bedrooms.
The development and use of BIM has assisted the volumetric supplier in their manufacturing sequencing. The main contractors build sequence is in reverse to the factory production and the use of 3D software has aided CIMC with their craned elements installation onsite – assessing loads and forward logistics planning. The BIM element enables early resolving of traditional interfaces e.g. with the in-situ blockwork lift shaft within a module, as well as coordinating the distribution of services within the ever-shrinking bathroom risers.
The benefits of container modular volumetric are still evolving in the UK market. CIMC continue to develop their own use of BIM in designing and procuring their modules, and the Bristol project illustrates the importance of choosing a rectilinear building with a high degree of repetition.
To continue reading this article, visit: Offsite Magazine Issue 12
Stackable and Repeatable
16th August, 2018
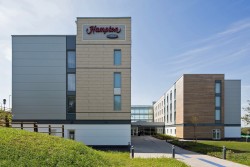