Prefab building techniques are being used to develop sustainable dwelling places at both ends of the size scale.
As the market becomes increasingly mindful of environmental issues, prefabricated building solutions are acquiring greater prominence because of their heightened efficiency and convenience.
A key example of this is a new concept design released by German firm Weingartner Architects for a prefabricated high-rise apartment building made primarily from timber.
The Woodscraper II concept consists of nine sparely designed "sky cubes" stacked on top of each other in a slightly staggered pattern and held in place via cantilevering from a central concrete core.
The central core that props up the sky cubes in place can contain as many as five smart elevators, as well as emergency stairs and plumbing and power infrastructure.
The tower would reach a height of up to 200 metres and be capable of accommodating over 300 residents - a number chosen by the architecture firm because "history shows that 300 people build a happy, strong lasting community that works."
The sky cubes would be prefabricated on the ground first for increased convenience and reduced cost, and only installed upon their cantilevered positions around the core following payment.
Sky cube installation process
This can help diminish investment risk for all parties, as well as hasten the pace of completion once the decision to purchase or occupy an apartment is made.
In order to raise the sustainability chops of the apartment building, Weingartner has also added other features including off-the-grid electricity, supplied by a wind turbines and solar panels in tandem with a combined heat and power station; an automatic heat recovery ventilation system, an electrochromic LED facade and an air thermal heat pump.
The enhanced efficiency and sustainability of prefabricated building solutions is a key factor in their rising popularity. Prefabricated building can cut down on needless wastage of materials, and thus significantly reduce the impact of the overall construction process on the environment.
This is also of benefit to the bottom line of developers, who derive additional economic advantages from the briefer construction times and reduced labour costs made possible by offsite construction.
These advantages have recently been exemplified on the other end of the size scale by the Castlemaine Passivhaus project in Australia.
The Castlemaine Passivhaus encompasses just 39 square metres of area and took a similarly modest amount of time to complete, with construction wrapped up in just 10 days by means of prefabricated building techniques.
The prefab sections were delivered to the site on the very day that the external structure was assembled, with the home ready for usage immediately following the 10-day construction period.
Australian architecture firm Carbonlite designed the compact home in order to demonstrate that Passive House sustainability certification can be obtained by dwelling places at the smaller end of the size scale.
The home achieves high levels of efficiency via a Sanden air-to-water pump for heating purposes, and a Lunos ventilation system which delivers a high air tightness performance of under 0.6 air changes per hour.
The total energy demand for the annual heating, electricity and hot water needs of the house is just 115 kWH/square metre, much of which is satisfied using solar PV panels.
The economic benefits of prefab building during the construction phase can be even further enhanced in Australia by leveraging the low-cost advantage provided by manufacturers in nearby mainland China.
Some Chinese companies are offering to sell a complete 75 square metre home unit from China for as little as US$13,000 via online vendors such as AliBaba. The price tag includes all plumbing and electricity.
Resources companies in Australia are already using prefab homes ordered from China for transit accommodation purposes in regional towns close to mining sites. The cost of the imported prefab homes are a fraction of that for existing alternatives.
Extensive alterations to the imported prefab units may be needed, however, to ensure that they comply with Australia's more stringent building codes.
Prefab Building Makes for Sustainable Homes of All Sizes
7th April, 2015
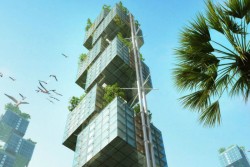