Call it what you will; ‘offsite construction’, ‘modern methods of construction’, or ‘industrialised construction’ is seen by both key industry players and government as crucial to improving the sector in terms of efficiency, cost, quality and sustainability – not to mention meeting the current housing crisis.
Offsite rises up the agenda
Indeed, at National House Federation’s annual conference in September 2014, Brandon Lewis, Minister of State for Planning and Housing, urged the housing sector to adopt offsite construction methods, telling the audience that it would help to both improve quality of new homes but also deliver them more quickly.
According to a survey conducted by Inside Housing magazine published in March, over the next three years, 56.8% of 22,544 homes planned by 17 of the UK’s largest housing associations will be constructed using offsite methods, including timber frame and modular construction. It follows a call in October 2014 by the Hyde Group housing association, which has 55,000 homes for market institutions to support offsite by allowing properties built using modular technologies to qualify for mortgage support on the same terms as traditionally built homes.
Meanwhile the Department for Business Innovation and Skills awarded £22.1 m grant to a consortium led by Laing O’Rourke to develop advanced methods for the manufacture of homes, buildings and infrastructure. It is part of the four-year, £104 m Advanced Manufacturing Supply Chain Initiative.
Bridging the knowledge gap
According to government figures, the offsite construction sector is currently accounts for 7% of total construction output in the UK, worth more than £1.5bn to the economy. Yet despite the rapid re-engagement with offsite following the recent downturn in construction, the main barrier to further adoption of offsite construction techniques is the lack of knowledge and skills among the supply chain. For example, a report published by the London Chamber of Commerce & Industry (LLCI) and KPMG last year pinpointed a lack of adequate understanding and training in modern methods of construction as a major worry and threat to London’s construction growth.
Which is why Peter Hansford, Government Chief Construction Adviser, lent his weight behind the Offsite Management School, which was launched to a packed audience on 24 March. A cousin to the Supply Chain Management School, the Offsite Management School, has received £180,000 from the UK Commission for Employment and Skills (UKCES), match-funded by industry partners to drive up skills.
It consists of online resources, e-learning modules, workshops and events, which are all free of charge to users and enable suppliers to benchmark their current knowledge of advanced construction and manufacturing techniques, plus assess their organisation's management skills. The School will also offer a network of expert advisers from within the industry, who can help members with practical support.
Collaboration and delivering Construction 2025
Crucially, the School is intended to help the sector to meet the challenges set out in the Construction 2025: to create buildings and infrastructure that has 50% less CO2 emissions; are delivered in half the time; and will cost 33% less to build and operate over their lifetime. And at the heart of the 2025 strategy is the recognition that the industry needs to swap its confrontational model with a more collaborative approach.
Hansford certainly believes that while the construction industry had come a long way in terms of collaboration, it still has a long way to go. “The thing with offsite thinking is that it requires the input of all levels of the supply chain, right from the earliest stage. And that won’t work without collaboration across the supply chain.
It is a key concept recognised by Mike Putnam, President and CEO of Skanska UK, a founding Partner of the Offsite Management School, who said it would facilitate collaboration at project, programme and industry level.
“It will lead to the creation of a network of like-minded businesses with access to expert groups and people [enabling] us to work better together, driving use of industrialised processes and delivery on a just-in-time basis,” said Putnam, emphasising offsite manufacturing’s role in helping the sector deliver the Construction Strategy 2025.
As Skanska UK’s Chief Financial Operator Roger Bayliss told the audience: “The industry contributed to Construction 2025, we’ve got skin in the game, we need to deliver it”.
Original link - Building 4 Change
Image: Industrialisation flowchart, courtesy of the Offsite Management School
Offsite is key to Construction 2025
14th October, 2015
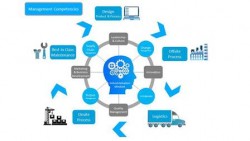