Whether referred to as ‘design for manufacture and assembly’, ‘offsite construction’ or ‘industrialised building systems’, these methods are possible panaceas addressing safety, productivity, quality, cost certainty and sustainability.
However, implementation of these techniques depends on collaborative working across the industry.
Design for Manufacturing and Assembly (DfMA) is a concurrent design and engineering process that focuses on meeting customer requirements while balancing cost, quality and performance.
In this approach, components are manufactured and preassembled in a controlled environment, prior to delivery to a construction site for installation. Unsurprisingly, the best results occur when DfMA is used in the conceptual stage.
It gives teams comprised of clients, designer and suppliers the chance to optimise the design for reducing waste and achieving efficiencies in terms of labour, build programme, carbon footprint and accident frequency.
Relationships building
During my time with Laing O’Rourke, I have witnessed a significant shift in how buildings and infrastructure are procured and delivered.
Negotiated opportunities, early contractor involvement and relationships with knowledgeable clients and consultants have helped us implement cutting-edge technology and develop the latest in construction innovation.
Having an offsite construction delivery partner alongside client design teams at concept stage aligns the design process with the client’s budget, unlocking significant opportunities to de-risk the project through efficiencies in not only design but also manufacture and construction, and delivers better whole lifecycle performance.
I believe this is the opportunity of a lifetime to change the image of our industry by collaborating early and building long-term, value-based relationships built on trust.
In the past we have been able to offer increased net saleable area through rationalisation of the structure, decreasing the volume of reinforcement required in precast components, and standardising components to cut the number and variation of elements.
All of this happened when the design was developing from RIBA stage two to four, eliminating the abortive works that would have resulted if these changes were made at late RIBA stage three or early stage four, which is when most traditionally tendered contracts are awarded to contractors.
Moreover, having detailed design plans means we have been able to build assets virtually using digital engineering and BIM and plan logistics to ensure programme surety.
Line of sight
Early knowledge of the constraints and boundaries within which offsite construction must operate allows design teams to align the structural, MEP and architectural offering with current manufacturing capabilities.
Furthermore, if a new technology or innovation is being considered, all stakeholders would have the opportunity to carry out robust technical due diligence to identify any unforeseen secondary effects.
This not only provides the client with programme, cost and quality surety, it is also the only way to foster innovation in projects and change the image of the industry in doing so.
The uptake of DfMA will undoubtedly grow. However, we need to form better collaborative partnerships between contractors, supply chain, design partners and clients.
Through collaboration with main contractors, the design partners need to understand the mechanics of offsite construction and build this into concept stage design. Contractors must then do more to communicate the value proposition of offsite manufacture.
Finally, clients need to articulate succinct output requirements and openly share affordability criteria and budgets.
The whole team must then invest more time in front-end design and planning such that construction methodology, logistics and test plans are well established and co-ordinated in digital engineering models prior to getting to site.
The face of construction is changing and I believe the construction professional of the future will not only work in collaborative multidisciplinary teams but will also be well versed in lean manufacturing and just-in-time delivery planning.
This will help deliver the step-change in our industry’s diversity, which is absolutely critical to developing the next generation of talent needed to deliver landmark projects.
DfMA engenders wider appeal by offering fixed workplaces, more flexible working, technical skills development and the opportunity to be at the forefront of innovation, showcasing the industry as an attractive and rewarding career choice for the very best and brightest.
Raj Kotecha is engineering project leader for Laing O’Rourke at Two Fifty One
Original link - Construction News
Offsite construction and collaboration can deliver a step-change
18th November, 2015
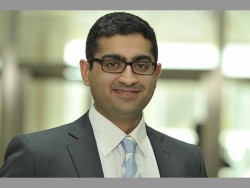