There are a huge range of offsite solutions available in the construction industry.
From large volumetric pods, ‘flat pack’ or panelised systems, through sub-assemblies that require some site work to ‘pre-kitted’ assemblies for site installation (think Ikea) - ‘offsite’ does not mean ‘pods’.
This provides solutions on a range of scales and degrees of sophistication, and the appropriate solution can be selected in response to the particular project drivers.
Offsite is not a constraint to design. Throughout history, the form of buildings and infrastructure has been reflected through the technology used to build them.
As recently as the ‘high tech’ movement, materials and fabrication techniques were celebrated as a key aesthetic and formed an integral part of the concept.
Meanwhile in the automotive and manufacturing industries, the adoption of new technologies is enthusiastically embraced; we are all benefitting from increasingly advanced phones, cars and other goods.
The best product design seamlessly brings together highly targeted functionality with cutting edge technology.
Up-front design
The opportunity to exploit the benefits of modern methods of construction therefore starts at the earliest stages of design.
However, all too often the use of design for manufacture is ‘post-applied’ to a fixed design, rather than forming one of the initial drivers. This can compromise either the underlying concept or the effectiveness of the offsite solution (or both).
Design for manufacture should be planned in from the start. At Bryden Wood we are exploring the architecture that comes from gaining a deep understanding of our clients’ current and future needs, using a wide range of analytical tools to develop strategic solutions that respond to business drivers.
The buildings and assets that we design are then able to benefit from best use of the available materials, products and techniques.
Leading the way
As we move towards ‘on site assembly’, rather than ‘construction’, we are developing assets that are more agile, flexible and responsive to current and future needs and this is reflected in their form.
BIM could be the catalyst for change. The strategy document Construction 2025 sets some key targets for the efficiencies in construction and operation.
While BIM on its own will not meet these targets, by facilitating collaborative ways of working it may act as a springboard that allows the efficiencies achieved in the manufacturing sector (in design, supply chain engagement, logistics, productivity etc.) to be successfully transferred to construction.
Rapid delivery of projects in China has become a YouTube staple, and adoption of design for manufacture is set to increase dramatically in places such as Singapore.
So, if we don’t do it, someone else will. Through initiatives such as Digital Built Britain the UK industry has the opportunity to capitalise on the current momentum and adopt design for manufacture to gain a competitive advantage in the global market.
Jaimie Johnston is director at Brydenwood
Source: Construction News
Lessons learnt from 20 years on the front line of DfMA
6th May, 2015
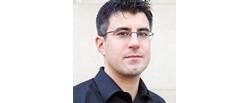