Back in 1998, Sir John Egan’s government report Rethinking Construction recommended offsite construction as faster, safer, cheaper and of higher quality.
The ambitious targets, especially on sustainability, set out in the more recent Construction 2025 industrial strategy will also require new methods of construction if they are to be met.
As environmental standards such as BREEAM and Passivhaus continue to get more rigorous, prefabricated buildings can assist in meeting those quality marks – a world away from their 1970s predecessors.
The key is starting in the right way.
Design for life
With modular buildings, you have far fewer onsite deliveries and vehicle movements, drastically reducing your impact on the local area as well as carbon emissions.
In addition to these benefits, the reduced time associated with offsite construction can have huge environmental benefits.
Modular builds save you time because they need far fewer weeks to deliver on programme compared with traditional builds.
And the more complex the building, the more time offsite construction methods save.
BREEAM SUCCESS FACTORS
• Outstanding energy performance
• Site management and procurement
• Health and wellbeing ie indoor/external issues; noise, light, air and quality
• Transport
• Water consumption and efficiency
• Building materials used
• Air and water pollution
• Type of site and building footprint
• Ecological value, conservation and enhancement of the site
Buildings are manufactured in controlled environments without exposure to the elements and with processes much easier to control than on a building site.
The crux of why modular is able to deliver greener buildings (and all others for that matter) more quickly is because enabling works can be carried out and foundations laid while the building is still being designed and manufactured.
Depending on their complexity, the site can even be ready before the building.
Safe as houses
With 'responsible construction practices' part of the BREEAM 2011 New Construction assessment method, any safety benefits can contribute to an improved rating.
Taking far less time to build on site automatically means a reduced risk of contact with the public.
Factories are easier to monitor, more efficient in their policies and protected from the elements, which makes modular less subject to the vagaries of weather-dependent processes that so often cause havoc with traditional build programmes.
There are also benefits for your staff.
They can be better protected from working at height, for example, because some jobs can be better done when the module is at ground level during the design stage.
Model builder
The benefits are clear.
As an industry, we're getting better at building better buildings – a trend set to continue, given the direction in which regulation is headed.
The government is leading the way – if you want to build a public building, you need to be fluent in BIM, CDM and modern methods of construction.
Standards are moving upwards, as witnessed with the launch of the new BREEAM standards and the improvement in U-values.
Offsite construction accommodates these changes more easily, and can play a significant role in helping a building achieve sustainability accreditation.
Jim Gowan is design manager at Roan Building Solutions
Source: Construction News
How to rapidly meet environmental standards with offsite
21st May, 2015
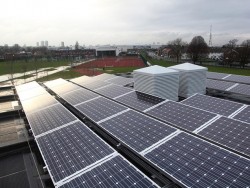