The role offsite manufacture can play in securing a healthier housing sector has never been more important. A pivotal provider of offsite timber housing systems is Stewart Milne Timber Systems (SMTS) who recently hosted a Roundtable Event to discuss future housing challenges and how to develop a maturing market.
The need to provide more homes of all tenures and types across the UK is well understood but perhaps even more important is to raise the standard of delivery and building quality. It is here that offsite manufacture is marking itself as a clear step-change to the traditional – and for many commentators – the tired way of building. Undoubtedly a boost has come over the last 18 months with the endorsement of central Government through its Housing White Paper and the London Assembly in particular on the requirement to embed a greater percentage of offsite manufacture in project assessments.
The Housing White Paper published in February 2017– Fixing our Broken Housing Market – recognised that change is a necessity and promised a broad range of ‘radical, lasting reform’ on the ways homes are delivered. Ultimately the Government can only do so much, but could an additional push for greater Government involvement with policy and legislation accelerate offsite uptake further?
“The Government has made it very clear since the White Paper that offsite is the way forward,” says Michelle Hannah, Director at Cast Consultancy. “From a policy perspective and in particular planning, I think there needs to be more work done on educating what offsite construction actually means. Sometimes the time taken to process a planning application actually hinders one of the key benefits of using offsite.”
Technology Talks
It would seem that for those unfamiliar with offsite technology, a wider rollout of training is required – through a wider factory tour programme – so offsite technology is not seen as an isolated process, irrespective of it being based around timber, steel or concrete. This skills deficit and lack of knowledge can be viewed at many different levels. Whilst many visual aspects of the design process and architectural approach are easier to digest, there is not enough concentrated efforts on understanding the structural and ‘precision engineered’ ways that buildings are created within the factory environment.
Gaps persist on what offsite can do. But most developers and housebuilders are savvy enough to know a greater percentage of factorydriven building design should be part of what they offer – without the government having to tell them. Major volume housebuilders are already seeking to increase the amount of offsite as a business necessity. “The drivers are well understood and are there already. We are adopting more offsite because we need to,” says Oliver Novakovic, Technical and Innovation Director for Barratt Developments. “Many construction site managers are still only attuned to brick and block and don’t understand enough about offsite, so where Government can possibly help more is with pushing some construction cultural changes.”
To continue reading this article, visit: Offsite Magazine Issue 12
Evolution Not Revolution
10th August, 2018
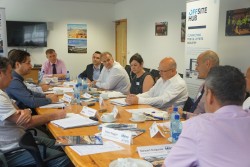